Next Generation Inactivation Technology
eFIT – KyooBe Tech’s revolutionary product series for inactivation of pathogens
in pharmaceutical production processes. By using low-energy electron irradiation (LEEI)
the genetic material of pathogens and cells in a liquid solution is reliably destroyed.
human and veterinary vaccines
cell and gene therapy
blood products
Our USPs
Our USPs
eFIT is a real game changer in vaccine research and manufacturing. Its advanced
features are reshaping processes and offer innovative possibilities for the future of
vaccine development. Discover them here.
The key USPs of eFIT include lightning-fast inactivation (≤ 1s), scalability in throughput,
and a commitment to chemical-free operation.
Fast inactivation time < 1 s
Scalable system
No toxic chemicals
The eFIT Lab Platform
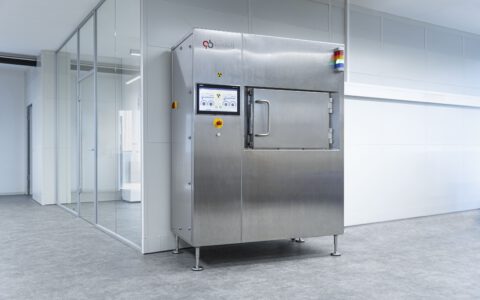
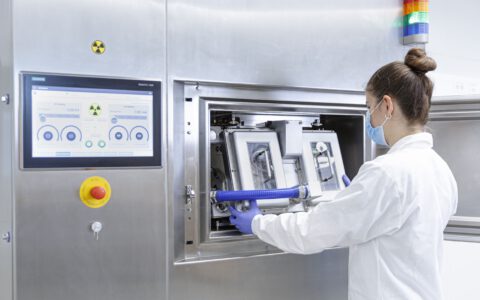
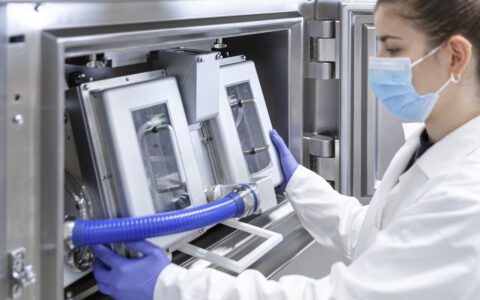
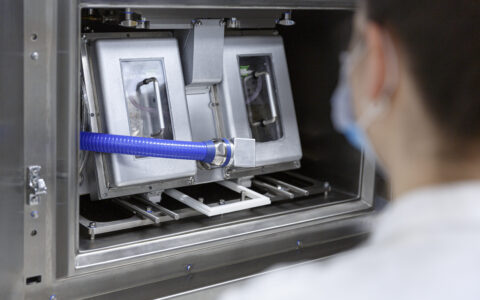
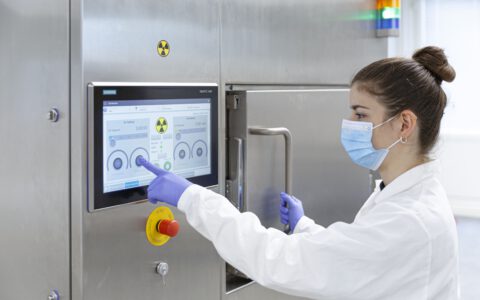
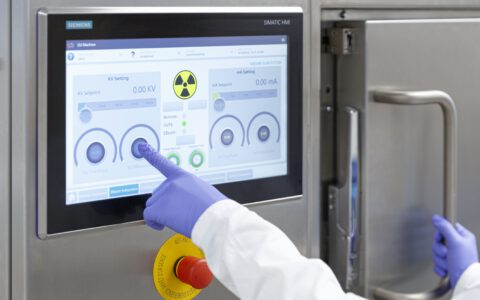
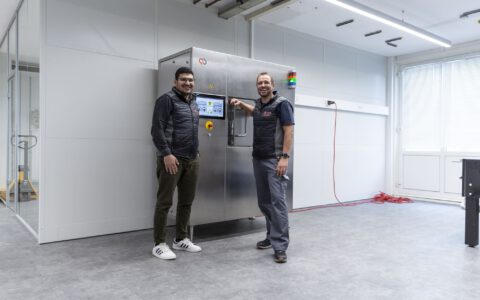
eFIT series: high-speed pathogen inactivation, large versatility for labs and industry, designed for your needs
Our Unique Approach
The Principle of the Inactivation Process
Targeted Low-Energy Electron Irradiation (LEEI) disrupts and neutralizes the pathogens‘
DNA or RNA. This ensures effective inactivation, as the pathogens‘ outer proteins remain
intact, but their reproducibility is disrupted.
Our Technological Approach
Irradiation of liquid solutions in a safe chip-based closed process.
Pathogens are irradiated with a defined energy dose [kGy].
Expert Feasibility Studies
The eFIT Lab unit stands as a testament to innovation, featuring a robust 6 log level pathogen reduction capability, for automated process testing in both vaccine R&D, cell therapeutics and in contamination control strategies (CCS).
We invite you to explore eFIT Labs potential through our expert biotechnologists and testing platform. Our commitment extends to comprehensive feasibility studies, offering you a unique chance to compare your existing method with the advanced LEEI technology.
Feasibility Studies as our Service
Testing of:
- pathogen suspensions
- virus suspensions
- blood derived products
- various other media and supplements
- pathogen suspensions
- virus suspensions
- blood derived products
- various other media and supplements
Expert Feasibility Studies
The eFIT Lab unit stands as a testament to innovation, featuring a robust 6 log level pathogen reduction capability, for automated process testing in both vaccine R&D, cell therapeutics and in “contamination control strategies” (CCS).
We invite you to explore eFIT Labs potential through our expert biotechnologists and testing platform. Our commitment extends to comprehensive feasibility studies, offering you a unique chance to compare your existing method with the advanced LEEI technology.
Feasibility Studies as our service
Testing of:
- pathogen suspensions
- virus suspensions
- blood derived products
- various other media and supplements
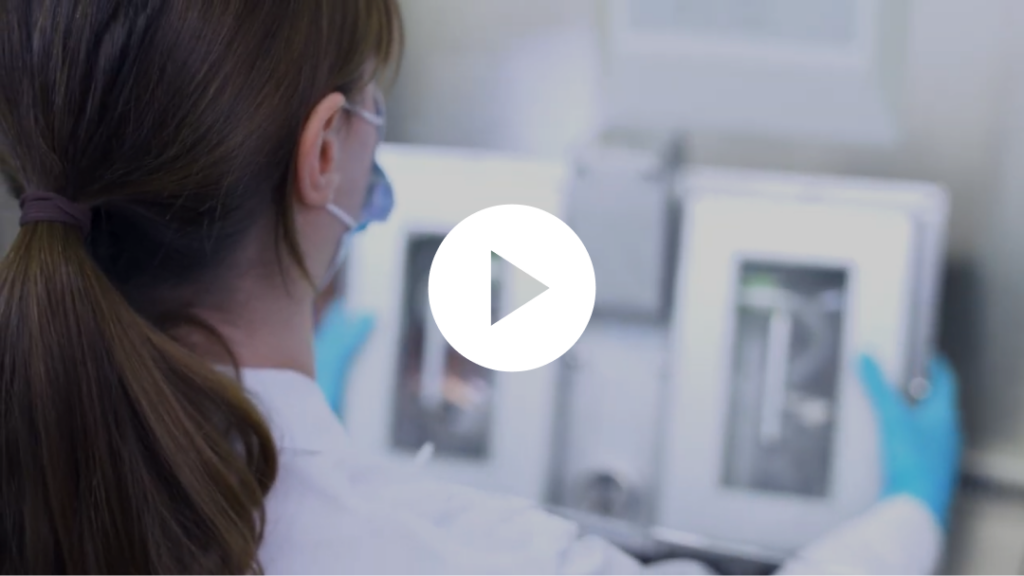
Discover The Opportunity: Feasibility Studies
Explore the unique opportunity to test our eFIT Lab unit.
Our feasibility studies offer a hands-on opportunity to discover the potential applications of this cutting-edge low-energy electron irradiation solution.
Gain valuable insights into the impact on the efficiency and safety of your vaccine production. Join us with this chance to be at the forefront of pharmaceutical innovation.
The Advantages & Benefits of Low-
Energy Electron Irradiation (LEEI)
Traditional pathogen inactivation methods involve time-consuming and potentially
hazardous chemicals like formaldehyde or beta-propiolacton. This process not only
generates toxic waste but also damages antigenic proteins, reducing immunity levels in
patients.
To address these issues, repeated booster vaccinations, larger amounts of starting
material, and efficacy enhancers like adjuvants are employed, leading to increased costs
and potential social acceptance challenges due to fears of side effects.
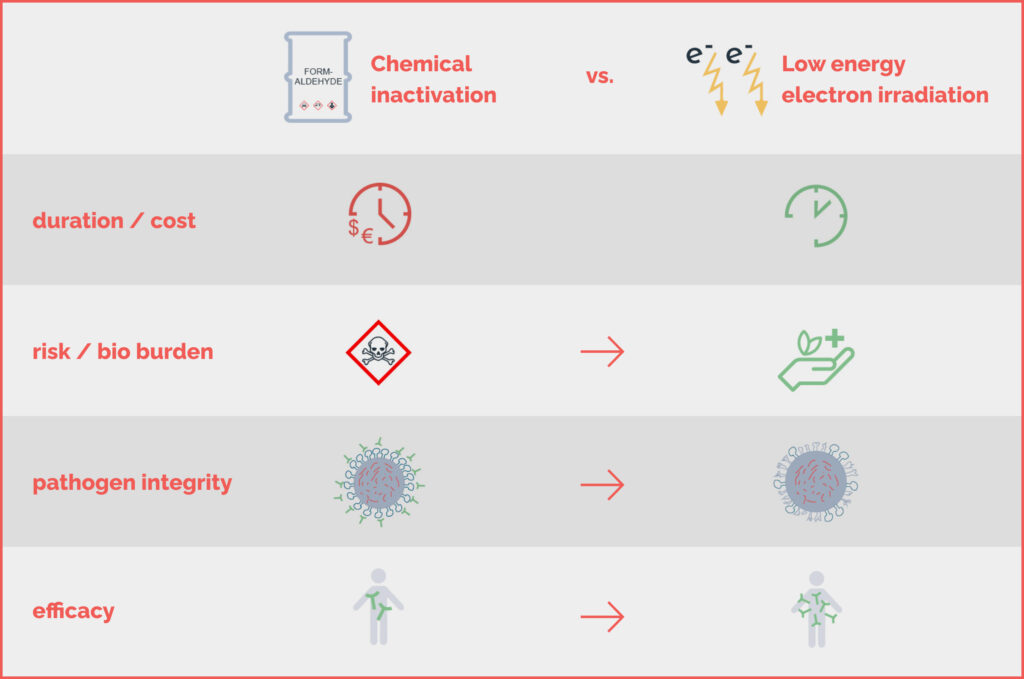
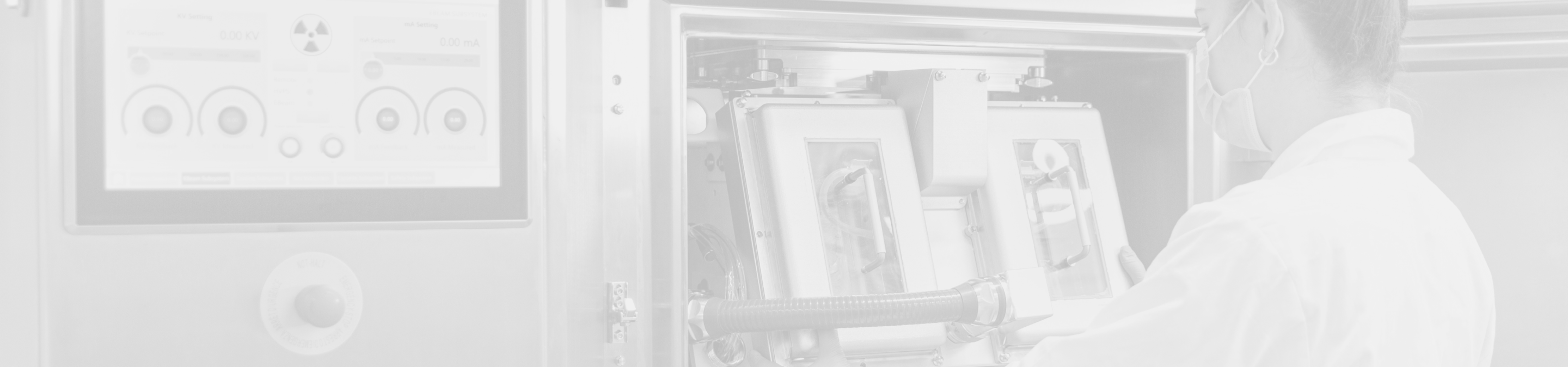